Environment
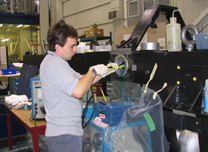
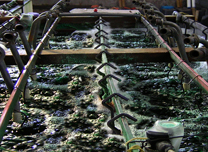
The Brush Plating process also has huge environmental advantages over conventional Tank plating methods. Although all plating processes require the build up metal to be in a liquid or solution form, there is a vast difference when comparing the two processes.
- Tank plating requires the parts to be submerged throughout the plating process. The tanks need to be as big as the largest part being plated. Depending on the operations, these tanks can range from 50 gallons to 1000’s of gallons of chemical plating solutions.
- Brush Plating requires considerably less material to accomplish the same results as other plating operations. A typical repair will require less than 2 litres of plating solution to be used.
- Brush Plating chemicals are designed as operator and environmentally friendly products that exclude such produces as cyanide or carcinogenic brighteners which are typically used in Tank plating.
- Brush Plating materials are deposited at ambient temperatures and normally do not exceed 100°F during operation. Generally, Tank plating procedures requires temperatures around the 140°F, and produce heavy toxic fumes.
- Conventional Tank plating systems require blowers to be used to expel the toxic fumes from the plating tank and away from the operator. The toxic fumes exit from the open top of the plating apparatus and are released to the environment, which is a health hazard and with highly undesirable results.
- Due to the large volume of toxic material involved in Tank plating, expensive and complex effluent systems are required in order to treat the liquid prior to it entering the public waste water system.